The School District of Palm Beach County, Florida - Other School Department Based Activities
Celebrating 10 Years Of Wellness
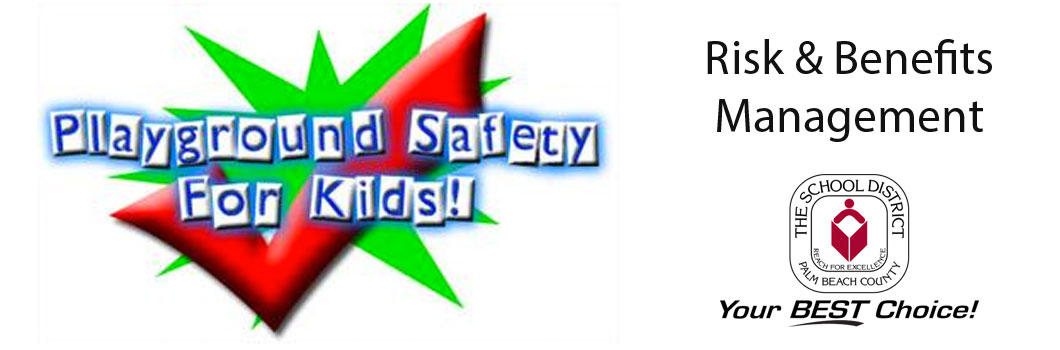
Playground Safety
Playground accidents account for roughly 50% of all student accidents at the Palm Beach County School District. Minimizing the cause of these accidents requires a focus on two areas. The first is ensuring playgrounds are maintained in accordance with national standards and manufacturer’s specifications. The second is properly supervising students as they play on the playgrounds.
Five years ago Risk Management & Facility Services began a new effort to maintain the playgrounds at our schools. Prior to 2010 the certified playground safety inspectors (CPSI) working for Risk and Benefits Management would inspect District playgrounds annually to determine compliance with American Standards for Testing & Materials (ASTM) and Consumer Product Safety Commission (CPSC) requirements. The inspectors identified and documented hazards observed during these inspections in the comments section of a District form. The forms were submitted to Facility Services for review and action. Reports were translated into work orders and were then worked on by the Grounds Department however there was no prioritization of work. Work was often done based on the volume or numbers of work orders that needed to be completed vs. the severity of the hazard that needed to be fixed.
This process was inefficient. Playground work orders were mixed in with other work orders at each location. As a result, playgrounds often didn’t get fixed in a timely manner. For example, minor hazards such as a guardrail that needed tightening, would turn into a missing guardrail a year or two later. Damaged vinyl coating on decking turned into rotting decking in a few years. Cracked poured in place rubber surfacing turned into damaged surfacing that no longer met original specifications at the time of installation.
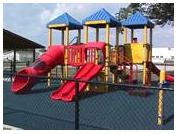
In 2010, this effort resulted in a changed approach to the way playgrounds were maintained. The first change was to assign a main point person in Facility Services to oversee playground maintenance. The next was to task that person with assessing the physical condition of all district playgrounds. This was done by creating a simple point system so that the playgrounds could be graded based on the condition of surfacing & equipment. This was strictly a physical assessment and had little to do with nationally recognized safety standards (e.g. ASTM or CPSC). Low scores resulted in a GOOD rating, slightly higher scores resulted in a FAIR rating and high scores resulted in a POOR ranking.
During the inspections additional items were documented including but not limited to the playground manufacturer, date of installation, and the type of surfacing used. The positive results from this survey included;
- The District now had an accurate accounting of the types and locations of each playground at each school.
- Facility Services was able to prioritize purchasing and maintenance decisions based on assessment results. This included projects related to;
- The entire replacement of aging playgrounds
- Replacement of parts, including decking, guardrails, & barriers
- Refurbishment, repair or replacement of playground surfacing materials.
- The ability to procure manufacturer warrantied parts
Risk Management & Safety- Playground Safety
As the inspections were done a playground work crew was assembled in Facility Services. This crew was tasked with fixing all playgrounds in the District based on a prioritized work order system that was created. The purpose in having a dedicated work crew for playground repairs was to ensure that they were all fixed in accordance with manufacturer’s specifications and applicable safety standards.
The second part of this project was to work with Risk Management to improve the methods used to report findings in the annual safety inspection reports. The previous system did not lend itself to prioritizing hazards. Collaboration between the two departments created a priority ranking system. The agreed upon hazard rankings were;
1 = “Unacceptable” likely injury or major damage – Must mitigate
2 = “Undesirable” some injury or equipment damage – Should mitigate
3 = "Acceptable" minor maintenance or adjustments – Schedule maintenance
ASAP
4 = "Questionable" code issues or disciplines beyond knowledge of inspection –
Review Required
The ranking system was tested during 2011 and became an official part of the inspection process in 2012. The ranking system allowed the playground lead person to prioritize hazards that needed immediate attention compared to those that were a lower priority. The system also allows the scheduling of other repairs based on the availability of parts and manpower. In 2015 the ranking system was revised to reflect the descriptions shown above.
Over the last five years the number of Category 1 and Category 2 hazards have continued to go down. The reduction in both categories continues to be between 70% & 60%.
National statistics indicate the # 1 and #2 causes of playground accidents are poorly maintained equipment and supervision. To address this Risk Management has developed two playground safety training videos. The first in the series deals with conducting monthly playground inspections and the second deals with improving playground supervision.
As the maintenance has improved over the past five years, the #1 cause of student accidents in the District during recent school years has been inadequate supervision. To address this the District is mandating that all elementary teachers take the online Playground Supervision course before the start of the FY17 school year.