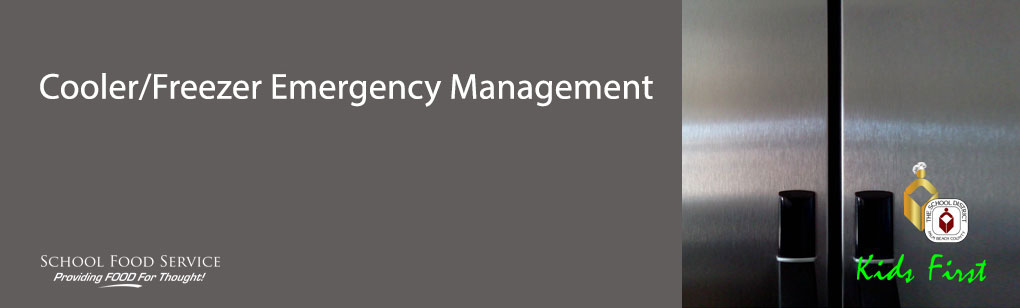
Cooler/Freezer Emergency Management
Upgrade hardware and software an perform training for cafeteria managers and central office to prepare for future technology opportunities - Ongoing
s
EMS Monitoring Systems
Two years ago School Food Service (SFS) met with the District’s Utility Manager to discuss an Energy Management System (EMS) specific to power supply and temperature monitoring of our kitchen walk in coolers and freezers. The objective was to identify and incorporate an EMS system so that we meet Hazard Analysis and Critical Control Points (HAACP) and USDA requirements. We cooperatively identified 24 sites that were not currently being monitored. School Food Service requested estimates from a vendor (Wisch & Jackson), who had the monitoring contract for the equipment and installation needed to set up the system for each site. Separate estimates were required; one for equipment monitoring and one for installation. In calculating costs, it was determined that the use of in-house labor to provide the installation of these systems would be more cost effective than outsourcing.
Our SFS Equipment Team electrician worked cooperatively with the Maintenance & Plant Operations (M&PO) and the Data Management Systems (DMS) staff to install the monitoring systems which required data and electrical supply to be installed in order to bring them on-line and operational. A schedule was developed to install a system at an average of one system per month. This schedule was based on work load of staff during normal operating hours and necessary time needed to install the components and connect power and data.
The 24 installations were completed at the end of April 2016. Wish & Jackson finished bringing systems on-line and completed monitoring capabilities on these systems by the end of June 2016.
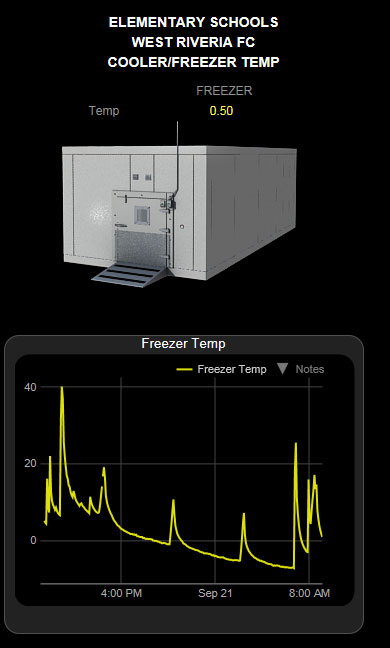